Shipyard
Fairing: Hull preparation and autonomous
surface work process
Fairing processes, including the application of sprayable filler, milling, grinding, and spray painting, currently demand significant manual labor. Traditionally, fairing a vessel has focused more on the end product rather than innovating the process, which remains labor-intensive, hazardous, and consumes large quantities of materials. The procedure is predominantly manual, highlighting the need for evolution towards safer and more efficient methods.
Time to change after 90years of traditional methods?

The Problem
Historically, the fairing of vessels has been a product-focused task, with minimal advancements in the methodology itself. This traditional approach not only requires substantial amounts of material due to its manual application but is also known for being labor-intensive. Furthermore, it involves inefficient logistics and poses environmental concerns, underscoring the need for a more evolved and sustainable process.
The Solution
Our mission is to assist you. Our team, comprised of specialists from various sectors, is dedicated to enhancing our clients' processes. We aim to deliver value through automation, transforming traditionally hazardous and labor-intensive tasks into safer, more efficient operations. With ROBOSURF's automation solutions, you can surpass conventional performance standards and reach unprecedented heights of production excellence across multiple domains.
out of the box thinking
The Process
Automating hullwork with ROBOSURF can result in savings exceeding 50% in both time and costs
when compared to conventional methods. Discover the specifics with our ROI Calculator Tool here.

Teaching
Whether through a collaborative robot (Co-Bot) teaching method or a high-precision 3D laser scan, the process begins by specifying the robot's operational areas and its autonomous parking positions.
The 3D scan is particularly advisable for documentation purposes. It facilitates the creation of a filler map, enabling precise material calculations and thickness measurements of the filler in advance. This is crucial for hull work, ensuring the final shape is accurately achieved while accounting for any deformations.


Sprayfiller
The use of sprayable fillers sets new standards in terms of quality and speed. Our software controls parameters so that the thickness can be defined and the inclusion of bubbles can be avoided.
The amount of sprayable filler can be calculated with a higher accuracy in advance.
Mitlling / Grinding
The milling operation, known for its supreme accuracy up to 0.2mm, incorporates vacuum technology for a cleaner environment and utilizes our advanced compensation software, online or offline, to precisely achieve the shapes designed by your architects. Similarly, our grinding process, equipped with force sensors, ensures consistent surface treatment, optimizing sandpaper usage and reducing consumption. This method maintains uniform roughness and quality without risking defects, also benefiting from vacuum technology to maintain workplace cleanliness.
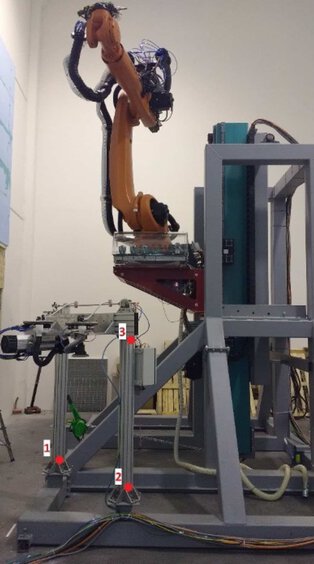
Traditional methods for Surface Finishing vs. ROBOSURF
ROI Example for the robot use case in Shipyards on just comparing the Hull Fairing process alone*:


*40% plus X reductions in time are possible. Further hard and soft benefits come on top.
Beyond the rapid ROI, ROBOSURF unlocks new levels of quality, health, safety, environmental sustainability, and increased productivity through 24/7 operations.
Explore the available ROBOSURF App Kits to expand your automation capabilities. Additionally, many countries provide extra tax incentives for investments in Industry 4.0 technologies like ours.
Investing in Co-Bots could see payback periods as short as 2-3 months. Interested in calculating ROI with a comprehensive view of your production, including materials, logistics, and overhead? Contact us, and we'll gladly share our detailed calculation model with you.